Scratch adhesion tester
The scratch tester - A simple coating adhesion test
One of the primary requirements of a PVD coating is excellent adhesion of
the coating to the
substrate, a property that can be defined as the interfacial forces between two surfaces. The most common method of assessing PVD coating adhesion is the scratch tester.
Scratch tester equipment
Scratch test - basics
The scratch tester moves a Rockwell diamond tip with a radius of 200µm across the
coated surface of a substrate at
a constant velocity while an increasing normal force is applied with a constant loading rate. The scratch test introduces
stresses to the interface between
coating and substrate causing delamination
or chipping of the coating. The critical normal force at which the first failure of the coating is detected is termed the critical load Lc.
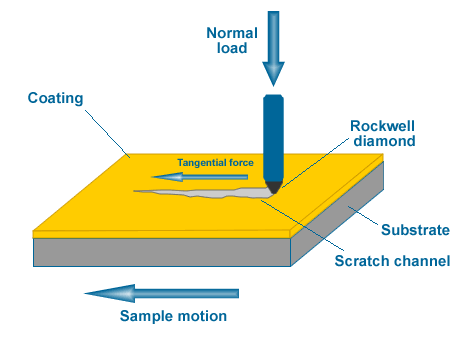
The scratch adhesion test
Scratch tester - Failure detection
The typical scratch tester has three methods of detecting coating failure; a load cell to measure the change in friction, acoustic
emission or observation of the scratch channel using an attached optical microscope. The best scratch adhesion testers use all three methods of coating failure detection. The intensity of the acoustic emission is dependent on the type of coating failure during the adhesion test e.g.
cracking, chipping (cohesive failure) and delamination (adhesive failure). It is therefore important to observe the coating failure after the adhesion test using an optical microscope to confirm the critical load.
Scratch test - Possible substrates
The scratch tester can be used to assess the coating adhesion on many different types of substrates such as metal alloys, semiconductors, glass, and refractive materials but is the most accurate when assessing the adhesion of hard coatings onto relatively hard substrates >54 HRC.
Example of the end of a scratch channel after a scratch test

|